Жижиг capacity ball mill
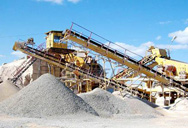
Calculate Ball Mill Grinding Capacity - 911
2015.10.15 The sizing of ball mills and ball milling circuits from laboratory grinding tests is largely a question of applying empirical
More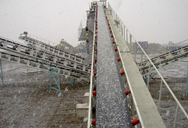
Small Ball Mill Capacity Sizing Table - 911
2016.2.14 Small Ball Mill Capacity Sizing Table. Do you need a quick estimation of a ball mill’s capacity or a simple method to estimate
More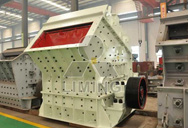
(PDF) Grinding in Ball Mills: Modeling and
2012.6.1 PDF The paper presents an overview of the current methodology and practice in modeling and control of the grinding
More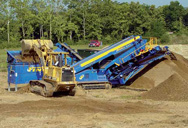
Ball Mill SpringerLink
2023.4.30 Ball mill is a type of grinding equipment that uses the rotary cylinder to bring the grinding medium and materials to a certain height and make them squeeze,
More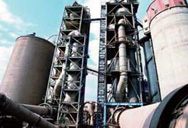
Ball Mill - an overview ScienceDirect Topics
A feature of ball mills is their high specific energy consumption; a mill filled with balls, working idle, consumes approximately as much energy as at full-scale capacity, i.e.
More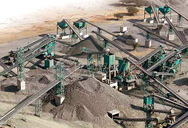
BALL MILLS Ball mill optimisation - holzinger
2021.3.12 in combination with a ball mill for cement grinding applications and as finished product grinding units, as well as raw ingredient grinding equipment in mineral
More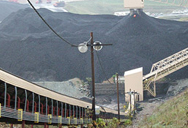
Analysis and Modeling of Key Data for Ball Mill Load in
Analysis and Modeling of Key Data for Ball Mill Load in Cement Grinding Process. Abstract: Ball mill load condition directly relate to the quality of cement products, use the
More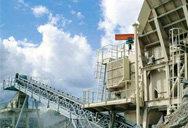
Ball Mill - an overview ScienceDirect Topics
The ball mill accepts the SAG or AG mill product. Ball mills give a controlled final grind and produce flotation feed of a uniform size. Ball mills tumble iron or steel balls with the ore.
More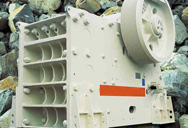
Large Ball Mill For Large Scale Mining And
Capacity: 15-615t/h. Motor power: 380-4500kw. Applications: It is widely used in mining, cement, metallurgy, building materials, ceramics, medicine and other fields. Email: info@ballmillssupplier. Get Price Now.
More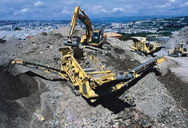
жижиг хэмжээний ball mill for
Construction and Working of Ball Mill - Solution Pharmacy. May 11, 2021The ball mill consists of a hollow metal cylinder mounted on a shaft and rotating about its horizontal axis. The cylinder can be made of metal, porcelain, or rubber. Inside the cylinder balls or pebbles are placed. The balls occupy between 30 and 50% of the volume of the ...
More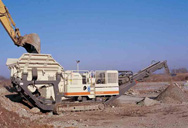
Ball Mill: Operating principles, components, Uses,
2022.11.30 A ball mill also known as pebble mill or tumbling mill is a milling machine that consists of a hallow cylinder containing balls; mounted on a metallic frame such that it can be rotated along its
More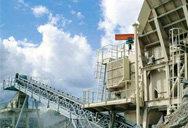
Small Ball Mill - 911 Metallurgist
1 天前 Small Ball Mills – Canada. We sell Small Ball Mills from 2′ to 6’ (600 mm X 1800 mm) in diameter and as long as 10″ (3000 mm) in length. The mills are manufactured using a flanged mild steel shell, cast heads, overflow discharge, removable man door, spur type ring gear, pinion gear assembly with spherical roller bearings, replaceable roller bronze
More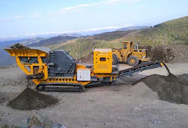
How to Choose the Right Types of Ball Mill for Your
The horizontal design makes it easy to operate and maintain, and it is suitable for both wet and dry grinding. 2. Vertical Ball Mill. A vertical ball mill is a type of ball mill where the barrel is vertical instead of horizontal. It is designed for fine grinding of materials, and it is usually used in laboratory or small-scale production.
More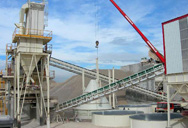
AMIT 135: Lesson 7 Ball Mills Circuits – Mining Mill
Mill Type Overview. Three types of mill design are common. The Overflow Discharge mill is best suited for fine grinding to 75 – 106 microns.; The Diaphram or Grate Discharge mill keeps coarse particles within the mill for additional grinding and typically used for grinds to 150 – 250 microns.; The Center-Periphery Discharge mill has feed reporting from both
More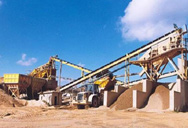
Ball Mill (Ball Mills Explained) - saVRee - saVRee
If a ball mill uses little or no water during grinding, it is a ‘dry’ mill. If a ball mill uses water during grinding, it is a ‘wet’ mill. A typical ball mill will have a drum length that is 1 or 1.5 times the drum diameter. Ball mills with a drum length to diameter ratio greater than 1.5 are referred to as tube mills.
More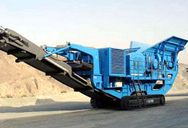
How Ball Mill Ore Feed Size Affects Tonnage Capacity
2017.7.26 As a result, the mill output will increase with this reduced size to approximately 77,000 tons per day. The gain in production compared to the 13,000 micrometer feed will be: (78,000 – 65,000)/65,000 x 100 = 20%. The theoretical gain will actually be greater because the graph in Fig. (21) is constructed according to the Gates
More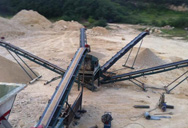
Ball Mills - 911 Metallurgist
2017.2.13 CERAMIC LINED BALL MILL. Ball Mills can be supplied with either ceramic or rubber linings for wet or dry grinding, for continuous or batch type operation, in sizes from 15″ x 21″ to 8′ x 12′. High density ceramic linings of uniform hardness male possible thinner linings and greater and more effective grinding volume.
More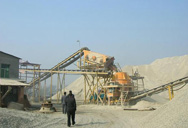
Ball Mill - Ball Mill Machine - AGICO
Ball mill is the key machinery for further smashing broken materials. Ball mill is suitable for crushing various ores for rotary kiln. Ball mill is widely used in many sectors like mineral processing, building materials and chemical industry. Ball mill can be divided into dry type and wet type; According to different mine discharge types, it ...
More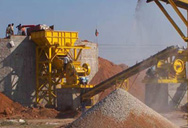
17 Signs of Problems with Ball Mills: Quickly Remove Hidden Troubles
2023.2.15 Here we list 17 signs to mention you that the ball mill is running and needs to be checked in. Find the abnormal signs early is very important to prolong the ball mill service life. 1. The sign of "swollen belly". Just like a bloated stomach, if the amount of grinding exceeds the maximum capacity and discharge capacity, it will cause the mill ...
More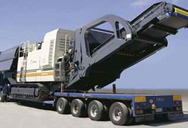
Ball Mill - an overview ScienceDirect Topics
Quantum Nanostructures (QDs): An Overview. D. Sumanth Kumar, ... H.M. Mahesh, in Synthesis of Inorganic Nanomaterials, 2018 3.6.1.1 Ball Milling. A ball mill is a type of grinder used to grind and blend bulk material into QDs/nanosize using different sized balls. The working principle is simple; impact and attrition size reduction take place as the ball
More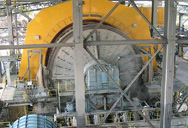
Planetary Ball Mill PM 400 - RETSCH - powerful
Planetary Ball Mill PM 400. The PM 400 is a robust floor model with 4 grinding stations and accepts grinding jars with a nominal volume from 12 ml to 500 ml. It processes up to 8 samples simultaneously which
More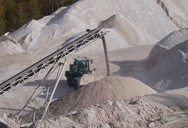
Hardinge Conical Mill Capacity - 911 Metallurgist
2017.4.10 6 ft. by 16 in. ball mill. Capacity, 150 tons per 24 hr., average of nine months. Charge, 4 tons of balls. Speed, 28 rev. per minute. Horsepower, 36. Water, 1.5 tons KCN solution to 1 ton of dry ore. Elevation of feed end, 1.25 in. Consumption of balls, 0.5 lb. per ton of ore. Feed to mill through 2-in. mesh.
More
(PDF) Grinding in Ball Mills: Modeling and Process Control
2012.6.1 A ball mill is a type of grinder widely utilized in the process of mechanochemical catalytic degradation. It consists of one or more rotating cylinders partially filled with grinding balls (made ...
More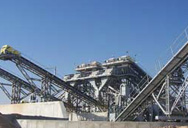
Factors Affect The Output and Quality of Ball Mills And How
2023.12.28 Many factors affect the output and quality of ball mills, which can generally be divided into three categories: process, mechanical, and management. From the perspective of production technology, the influencing factors are mainly the following 10 points: 1. Particle size of grinding materials. The grinding materials’ particle size affects ...
More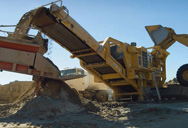
Understanding the SAG Mill in Copper Ore Mining Process
2023.10.10 A SAG mill, or semi-autogenous grinding mill, is a type of machine used in mining and mineral processing operations. It uses the crushing and grinding action of rocks to reduce materials such as copper ore into smaller pieces for further processing. Unlike traditional mills that rely on steel balls or other media to break down materials,
More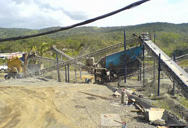
Ball Mill Rod Mill Design - 911 Metallurgist
2016.4.21 The apparent difference in capacities between grinding mills (listed as being the same size) is due to the fact that there is no uniform method of designating the size of a mill, for example: a 5′ x 5′ Ball Mill has a working diameter of 5′ inside the liners and has 20 per cent more capacity than all other ball mills designated as 5′ x ...
More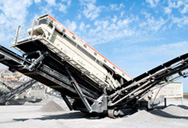
Analysis of mill capacity using a theoretically derived
Powder Technology, 58 (1989) 117 - 124 Analysis of Mill Capacity Using a Theoretically Derived Selection Function Applied to Ball and Hardgrove Mills S. NOMURA and T. TANAKA Department of Chemical Process Engineering, Hokkaido University, Sapporo 060 (Japan) (Received August 1, 1988; in revised form October 31, 1988) 117 SUMMARY
More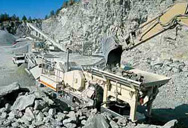
Planetary Mills Fritsch Milling and Sizing
2024.3.15 PLANETARY BALL MILLS FRITSCH Planetary Ball Mills – high-performance all-rounder in routine laboratory work. HIGH-SPEED AND VERSATILE Expand your capabilities with FRITSCH Planetary Ball Mills, used for the fine grinding of hard, medium-hard, soft, brittle, tough and moist materials. Useful in QA/QC, RD or
More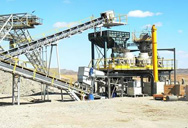
BALL MILL 1 KG - Bexco Exports
2019.1.1 Suitability for wider variety of commercial materials. 1.0 kg of capacity and variable 80-120 rpm speed. Runs on 220-240 V AC. Comes complete with country specific cable, stainless steel container
More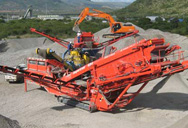
Exploring the Capacity and Specifications of Ball Mills
Capacity. The capacity of a ball mill is directly influenced by several factors, including the diameter of the mill, the length of the mill, the total weight of the grinding media, and the rotation speed of the mill. The diameter and length of the mill determine the volume of the mill, which is a primary indicator of its capacity.
More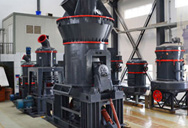
The Ultimate Guide to Ball Mills - Mining-pedia
2019.8.14 Reasonable steel ball grading is the key to maximize the grinding capacity of the ball mill, which will have a direct impact on the grinding efficiency, and then affect the ball mill output. In the production of the processing plant, the more common steel ball ratio of ball mill is two-stage ratio and multi-stage ratio. Generally speaking, the ...
More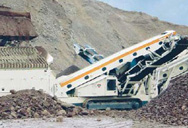
Ball Mill - SBM Ultrafine Powder Technology
Transmission device: The ball mill is a heavy-duty, low-speed and constant-speed machine. Generally, the transmission device is divided into two forms: edge drive and center drive, including motor, reducer, drive shaft, edge drive gears and V-belts, etc. 4. Feeding and discharging device: The feeding and discharging device of the ball mill is ...
More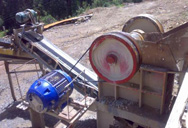
A Comprehensive Guide to Finding the Best Ball Mill for Sale
Tumbling ball mills: These mills are similar to vibratory mills but use a rotating drum instead of vibration to grind materials. Tumbling ball mills are often used for high-capacity applications and can produce very fine particle sizes, making them ideal for grinding pigments, chemicals, and other materials.
More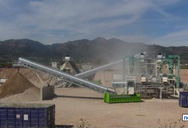
Automated grinding ball loader - MagoLoad Magotteaux
The MagoLoad is designed for automated grinding ball addition and on-line reporting in milling plants. The equipment insures grinding balls are added into the mill and taken into account for accurate control of ball consumption and related wear rates monitoring. Reduction of ball handling costs through decreased man hours and increased safety.
More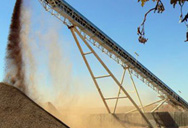
Ball Mill Grinding Theory - Crushing Motion/Action Inside
2017.4.28 The classifier delivered 33 T. of sand per hour. The total ball-mill feed was therefore 40.37 T. per hr. or 550 per cent, of the original feed. Two Stage Grinding. The object of these tests was to determine the capacity of ball-mills when crushing in two stages. The conditions of the test were as follows: First Stage of Ball Milling
More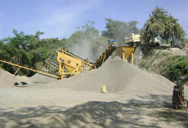
Ball Mill - Sand Ball Mill Manufacturer from Mumbai
Manufacturer of Ball Mill - Sand Ball Mill, Industrial Ball Mills offered by Anahit Engineering Corporation Raymer Engineering Corporation, Mumbai, Maharashtra. ... Capacity: 0.65 - 90 t/hr: Material: Mild steel, SS zeketed: Coating: MS or SS coating: Grade: SS 304: Discharging Granularity: 0.074~0.4 mm:
More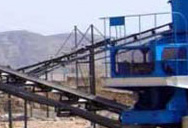
Charge behaviour and power consumption in ball mills:
The experimental assessment of ball mills type MCB 4.5x6 (МШЦ 4,5х6) operating in copper ore processing plant and SAG mill 8.5x5.3 operating in gold ore processing plant are presented. ... grinding will occur for a lower total energy consumption at a 40% fill level rather than one jammed to near or above capacity at 50%. This is consistent ...
More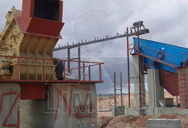
Ball Mill Design/Power Calculation - 911 Metallurgist
2015.6.19 The basic parameters used in ball mill design (power calculations), rod mill or any tumbling mill sizing are; material to be ground, characteristics, Bond Work Index, bulk density, specific density, desired mill tonnage capacity DTPH, operating % solids or pulp density, feed size as F80 and maximum ‘chunk size’, product size as P80 and maximum
More