ball mill output feed Хэмжээ
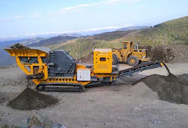
TECHNICAL SPECIFICATION OF WET BALL MILL
2022.3.29 The Gravimetric feeder feeds limestone to Wet ball mill system. The Wet Ball Mill system consists of Wet Ball Mill, Wet Ball Mill Lubrication system, Mill circuit tank
More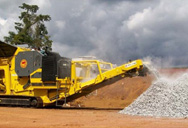
Ball Mill - an overview ScienceDirect Topics
The minimal magnitude of ball size is calculated in millimeters from the equation: where db.max is the maximum size of feed (mm); σ is compression strength (MPa); E is
More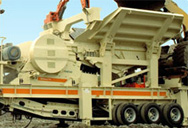
Optimization Of Ball Mill Feeding Device Design - ball
2023.2.20 1. Truncated Cone Funnel Feeding Design The feeding steps of this ball mill design feed are as follows. The ballmillssupplier info@ballmillssupplier Tel:
More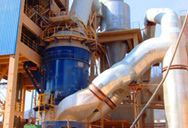
MODULE #5: FUNCTIONAL PERFOMANCE OF BALL
2018.12.9 As for any output, ball mill circuit output is a function of both its inputs and efficiencies. There are two "inputs" to a ball mill circuit: the ore fed to the circuit and the
More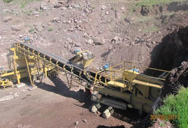
Tailoring ball mill feed size distribution for the production of
2019.9.1 This makes feed tailoring in ball milling an interesting parameter to investigate with the aim of maximising the desired mill product. To that end, batch tests
More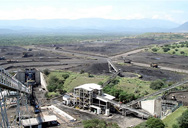
AMIT 135: Lesson 7 Ball Mills Circuits – Mining
A survey of Australian processing plants revealed a maximum ball mill diameter of 5.24 meters and length of 8.84 meters (Morrell, 1996). Autogenous mills range up to 12 meters in diameter. The length-to
More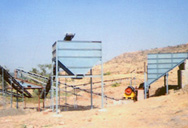
Design of Ball Mill Feeding System - cemteck
Abstract This article introduced the design method of ball mill feeding chute, air inlet duct, feeding sleeve and helix tube; by taking the ?4.2m×13m cement mill feeding system
More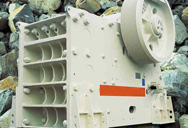
BALL MILLS Ball mill optimisation - holzinger
2021.3.12 Ball mills and grinding tools Cement ball mills are typically two-chamber mills (Figure 2), where the first chamber has larger media with lifting liners installed,
More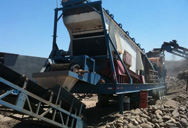
Effect of ball and feed particle size distribution on the milling ...
2018.6.1 Effect of ball and feed particle size distribution on the milling efficiency of a ball mill: An attainable region approach Semantic Scholar. DOI:
More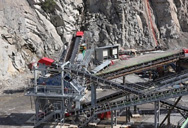
The Ultimate Guide to Ball Mills - Mining-pedia
2019.8.14 5. The size of the ball mill is large, and it is necessary to carry out lifting work during the process of replacing the ball mill liner. The hoisting ball mill liner is the responsibility of the hoist. The lifting process requires attention to the operation of the wire rope and the hook. 6.
More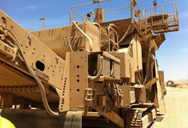
Circulating Load Equation - Grinding
5 天之前 To participate in the 911Metallurgist Forums, be sure to JOIN LOGIN; Use Add New Topic to ask a New Question/Discussion about Grinding.; OR Select a Topic that Interests you.; Use Add Reply = to
More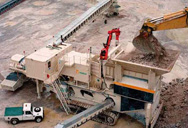
Ball Mill Design/Power Calculation - DESIGN AND ANALYSIS OF BALL MILL ...
2015.6.19 The bottom parameters used in ball milling design (power calculations), rod mill or any tumbling mill page is; material to be ground, property, Bond Employment Card, bulk density, specific density, wish mill tonnage capacity DTPH, operates % stables or pulp density, feed extent as F80 and maximum ‘chunk size’, product size as P80 and
More
Ball Mill Manufacturer - Henan Zhengzhou Mining
2021.7.16 Ball mill is mainly used for grinding in mining (metallic minerals and non-metallic minerals), cement, refractories, chemical, power plant, aluminum, building material, glass, ceramic, steel slag and fly ash, ect.It follows more crushing and less grinding principle to save energy. The feed size to ball mill shall be smaller than 25mm, the output size can
More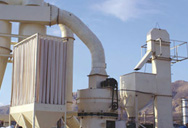
BALL MILLS Ball mill optimisation - holzinger
2021.3.12 Ball mills and grinding tools Cement ball mills are typically two-chamber mills (Figure 2), where the first chamber has larger media with lifting liners installed, providing the coarse grinding stage, whereas, in the second chamber, medium and fine grinding is carried out with smaller media and classifying liners.
More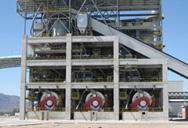
5 Ways to Improve the Ball Mill Efficiency - Fote
2020.1.11 Compared with other ball mills that used for the same period, his ball mill grinding efficiency is higher by about 25%. At present, the capacity of the gold ball mill is 180TPH, the particle size of the feed is controlled at about 20mm, and the output easily reaches 200 mesh. Gold ore working site
More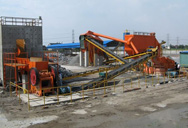
Ball Mill - Principle, Construction, Working, and More - Soln
4 天之前 Principle of Ball Mill: The size reduction in the ball mill is a result of fragmentation mechanisms (impact and attrition) as the balls drop from near the top of the shell. Mixing of feed is achieved by the high energy impact of balls. The energy levels of balls are as high as 12 times the gravitational acceleration.
More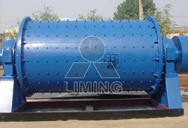
Ball Mill Feeders - 911 Metallurgist
2016.10.22 The entire mill feed enters the drum via a chute or spout and an internal spiral carries the feed into the trunnion liner. The drum feeder may be used in lieu of a spout feeder when headroom limits direct spouting. The drum also provides a convenient method of adding grinding balls to a ball mill. The drum is generally lined with Manganese Steel.
More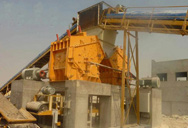
TECHNICAL SPECIFICATION OF WET BALL MILL
2022.3.29 Ball Mill, Wet Ball Mill Lubrication system, Mill circuit tank with an agitator, Mill circuit Pump, Mill Hydro cyclone, 3-way distributor and accessories. The Wet Ball Mill is the wet horizontal type. ... 4-20 mA output signals from transmitters/other control system shall be able to drive minimum 500 Ohms load resistance. The system shall be ...
More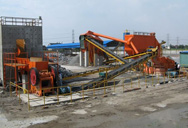
Ball Mill Grinding Machines: Working Principle, Types, Parts ...
A ball mill consists of various components that work together to facilitate grinding operations. The key parts include the following: Mill Shell: The cylindrical shell provides a protective and structural enclosure for the mill. It is often made of steel and lined with wear-resistant materials to prolong its lifespan.
More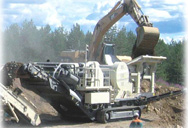
Remas Redüktör ve Makina
The required mill size and attributes can be determined by analyzing the ore characteristics, the feed size, the desired product size, the grinding circuit type and the desired hourly capacity and output. We are happy to work
More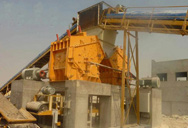
Estimation methodology for Bond ball mill work index experiment output ...
2023.10.1 The Bond ball mill work index test is a standard procedure to determine the ore grindability in function of specific energy (kWh/ton). This index is extensively used in the mineral processing industry and needs an available skilled staff and specially prepared feed samples (Aksani and Sönmez, 2000).
More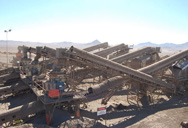
Ball feeder - Metso
Optimizing grinding mill performance. Metso's ball feeding technology utilizes a simple and robust design to continously and efficiently feed the grinding mill. With this in place, the grinding mill can operate at maximum
More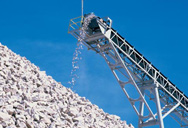
Effect of ball and feed particle size distribution on the milling ...
DOI: 10.1016/J.SAJCE.2018.02.001 Corpus ID: 139435815; Effect of ball and feed particle size distribution on the milling efficiency of a ball mill: An attainable region approach
More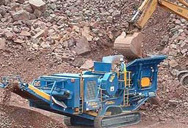
MODULE #5: FUNCTIONAL PERFOMANCE OF BALL
2018.12.9 The output of a ball mill circuit is therefore a function of two inputs and two efficiencies. This is illustrated in Figure 1. Figure ... During Survey #1 at the Camco Mine, the ore feed rate to the ball mill circuit was 67 t/h. The circuit feed contained 29.33% of -106 micron (150 mesh) material (fines) and the circuit product contained 78.54% ...
More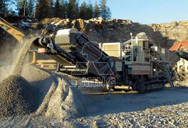
Ball Mill - [PDF Document]
2014.11.13 The types of ball mills: batch ball mill and continuous ball mill with different grinding. media and different design depend on the nature of the input material and the nature. of the output which I need. We discuss the types of ball mill, the basic principles of the ball mill, how it works,
More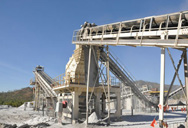
Effect of ball and feed particle size distribution on the milling ...
Effect of ball and feed particle size distribution on the milling efficiency of a ball mill: An attainable region approach. / Hlabangana, N.; Danha, G.; Muzenda, E. In: South African Journal of Chemical Engineering, Vol. 25, 01.06.2018, p. 79-84. Research output: Contribution to journal › Article › peer-review
More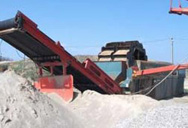
AG - Autogenous SAG Semi-Autogenous Mill Design Calculations
2018.4.17 Product Size: All passing 6 mesh with 80% passing 20 mesh. Net power from pilot plant: 16.5 KWH/ST. Mill, gear and pinion friction multiplier: 1.025. Mill Power required at pinionshaft = (240 x 16.5 x 1.025) ÷ 0.746 = 5440 Hp. Speed reducer efficiency: 98%. 5440 Hp ÷ 0.98 = 5550 HP (required minimum motor output power).
More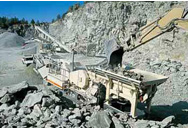
Ball Mill Used in Minerals Processing Plant Prominer
Ball mill Structure: Ball mill Advantages: 1、Jack-up device, easy maintenance; 2、The hydrostatic and hydrodynamic bearings ensure the smooth operation; 3、Low speed transmission is easy for starting and maintenance; 4、The oil-mist lubrication device guarantees reliable performance of bearings; 5、The air clutch adopts the flexible start ...
More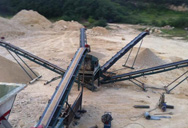
Ball Mill: Operating principles, components, Uses,
2022.11.30 A ball mill also known as pebble mill or tumbling mill is a milling machine that consists of a hallow cylinder containing balls; mounted on a metallic frame such that it can be rotated along its longitudinal axis. The balls which could be of different diameter occupy 30 – 50 % of the mill volume and its size depends on the feed and mill size.
More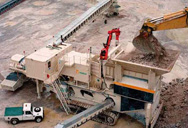
Industrial Ball Mill Grinders Pulva
Ball mill drums offer an efficient and inexpensive way to grind materials down to a more usable size, often as fine as 25-75 microns. Both continuous and batch style ball mills use centrifugal force, gravity and hard media to break up industrial materials into fine pieces or powder. Ball milling systems grind dry material and wet slurry alike.
More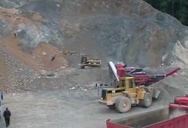
Ball Mill- Principle, Application, Uses, Critical
2023.2.25 The principle of ball mills is based on impact and attrition. The grinding media in the ball mill collide with each other, and the material being ground to produce a fine powder. The impact of the grinding media
More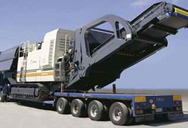
Output of Ball Mill - Liming Heavy Industry
This page is about Output of Ball Mill. Henan Liming Heavy Industry Science Technology Co.,Ltd. 0086-371-86162511; 0086-371-67992699; lmzz_jkj@break-day ... by wonder how effecient is the ball mill is, is there any calculation to determine the product of the ball mill, i.e a coarse particle input, how fine is the output particle is. Hope ...
More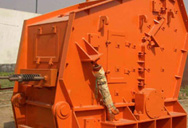
10 Ways to Improve the Grinding Efficiency of Your Ball Mill
2019.4.15 Here are the 10 ways for your to improve the ball mill performance: Step#1. Change the original grindability. Step#2. More crushing and less grinding to reduce the feed size into mill. Step#3. Reasonable filling rate of steel ball. Step#4. Reasonable size and proportion of steel ball.
More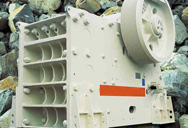
How to Improve Ball Mill Performance - 911 Metallurgist
2017.10.25 Ball Mill Breakage Efficiency. Consider a ball mill circuit processing material of a given feed size and at a given throughput rate to a target product size, the latter which once again distinguishes the “fines” from the “coarse” material. The production rate of fines or new product size material can be calculated from the circuit feed ...
More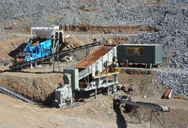
Ball Mill Ball Mills Wet Dry Grinding DOVE
3 天之前 DOVE small Ball Mills designed for laboratories ball milling process are supplied in 4 models, capacity range of (200g/h-1000 g/h). For small to large scale operations, DOVE Ball Mills are supplied in 17 models, capacity range of (0.3 TPH – 80 TPH). With over 50 years experience in Grinding Mill Machine fabrication, DOVE Ball Mills as ...
More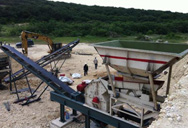
A comparative study on a newly designed ball mill and the
2020.1.1 The discharge end design of a ball mill plays an important role in discharging the desired particle sizes (−150 + 10 µm) and the percentage of recirculating load from the discharge end of the ball mill. In continuous wet ball mills, the composition of feed (hard ore or soft ore) to the mill varies continuously, leading to uncontrolled ...
More
Planetary Ball Mill PM 100 - RETSCH - highest fineness
The ideal Ball Mill for standard applications. Max. speed 650 rpm. Up to 10 mm feed size and 0.1 µm final fineness. 1 grinding station for jars from 12 ml up to 500 ml. Jars of 12 – 80 ml can be stacked (two jars each) GrindControl
More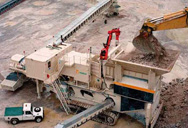
Estimation methodology for Bond ball mill work index experiment output ...
2023.10.1 A standard Bond mill (Fig. 1) was designed to perform the work index tests and determine the energy consumption of various s minerals.The mill has a round internal housing at the corners, has no lifters, and is for dry grinding. The inner diameter and the length are 0.305 m, and the ball load is 19.4% of mill volume (equaling a total weight of
More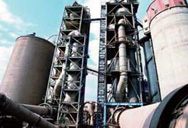
Ball Mill Operation -Grinding Circuit Startup Shutdown Procedure
2016.2.1 Normal Shutdown Sequence of Ball Mill and Grinding Circuit. Shut off cyanide metering pump. Put weight controller into MANUAL mode and turn controller output to 0%. Run the ball mill for 15-30 minutes. Put density controller into MANUAL mode, set output to 0%. Put flow controller into MANUAL mode and set output to 0%.
More